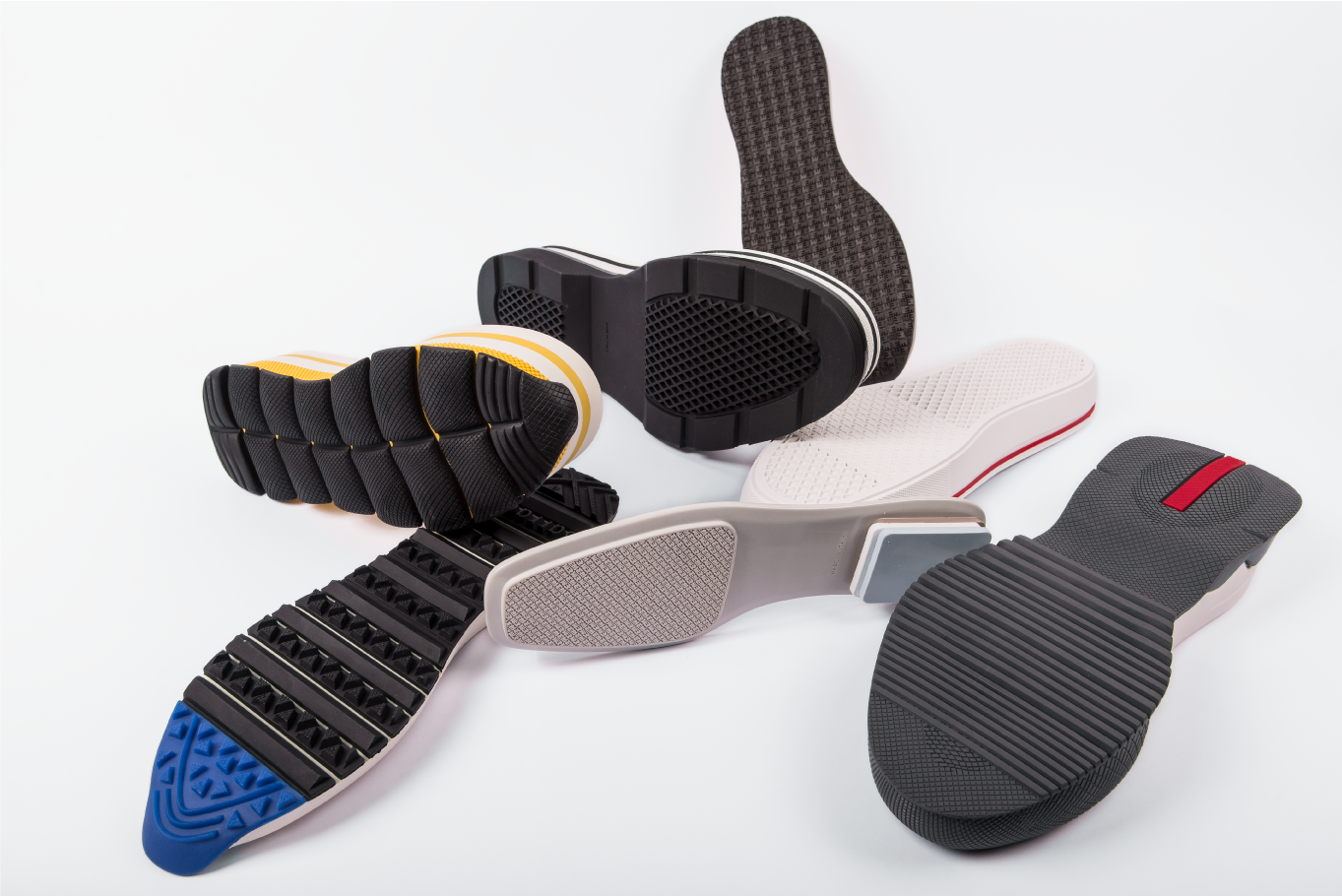
How is a Sample Set of Shoe Soles Created?
Stylistic research and product innovation are key elements in determining the success of a footwear collection. This is why we offer our clients a dedicated service for creating prototypes and fashion samples. Let’s explore together how a sample set of shoe soles is created.
What is a sample set?
A sample set is the prototype of an item not yet on the market, designed to showcase a new fashion collection or a redesigned product. It is used to evaluate the fit, material quality and manufacturing processes, allowing for adjustments before production begins. Creating a sample set is a crucial step in the fashion industry, representing the first model of a new product.
Just like a dress, a shoe starts with a designer’s idea, which is transformed into a sketch. This sketch goes through various stages involving multiple companies to become a finished product. We are part of this process, focusing on the shoe’s base: the sole.
Phase 1: Project consultation and mold design
Following an initial technical and economic consultation on the project, our technical department designs the mold, which is the negative shell of the sole, based on the sketch provided by the fashion company’s style office. The sketch can be a simple drawing or a vector file and can represent a completely new model or modifications to existing ones. Like the upper part of the shoe, the sole requires a detailed study of design, volumes, colors, materials and the type of support it will provide to the foot, considering factors such as lightness and durability. Once the sole template is determined, we proceed to prototyping, creating the model in rigid or soft material.
Phase 2: Prototiping
Prototyping is the simulation of the final sole, allowing the fashion company’s style office to see their ideas realized and evaluate their feasibility. Sometimes, a prototype may be discarded because it does not meet the designer’s expectations or involves overly complex and expensive processes. Prototypes also help identify any technical challenges during production. Each prototype is archived with a “prototype sheet” containing details such as season, year, model, drawing, type of processing and material consumption.
Phase 3: Construction of the mould pilot
Next, we create a pilot mold with a male and/or female numbering, depending on the model. The pilot mold usually corresponds to the middle size of the range: 37/38 for women, 42/43 for men, 31/32 for children.
Phase 4: Color references and sample sole
The style office and the client’s product office send us the color references they want to test before the shoe goes to market. Our sample manager develops the masterbatch and produces the first samples, perfecting all necessary processes such as molding, painting, foaming or assembling components. The sample sole is then sent to the client for approval. If approved, mass production begins and the signed sample sole is archived in our sample archive.
The unpredictable market trends and the relentless pursuit of innovation mean that client requests are increasingly unique. The search for new sustainable materials, trending colors and components make each client a world of their own, creating the distinctive character of the fashion company behind all our work.
- 28/05/2024
Share on social
Articles that may interest you